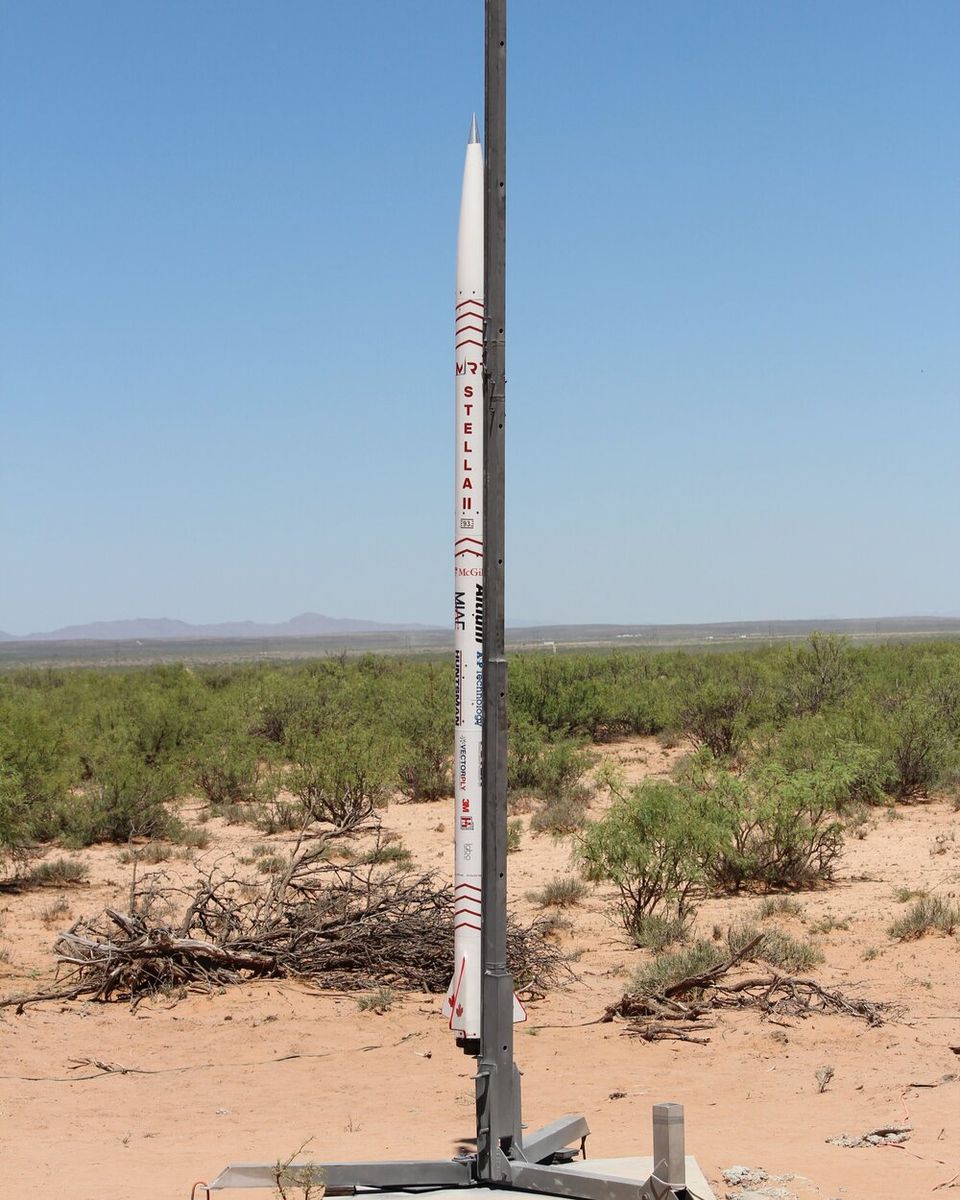
Project Stella II (2018)
Stella II 30K COTS
The 2018 IREC marks McGill’s 4th year participating in the competition. Stella II is the successor to Stella, the team’s first 30,000 ft COTS category entry. Following the off-nominal flight of Stella last year, the team has fundamentally reworked the recovery system design and airframe manufacturing process to prevent the same issues from reoccurring.
To further validate the changes, the team has built a secondary rocket, Bertrand, which flew on a test launch on June 2nd, 2018. However, manufacturing an entirely separate rocket to test critical recovery and avionic systems increased financial costs. In order to help offset the additional costs, the group expanded the number of student-made components, replacing off-the-shelf pieces. Only 3 of the 53 major components in Stella II were off-the-shelf - being the motor itself, the avionic redundancy, and a motor retaining ring. Student made components such as parachutes, shock cords, CO2 ejectors, tender-descenders, and the airframe lead to cost savings of several thousand dollars.
Stella II is divided into four main subsystems: propulsion, aero-structures, recovery and payload. The propulsion unit is an O-class Cesaroni motor.
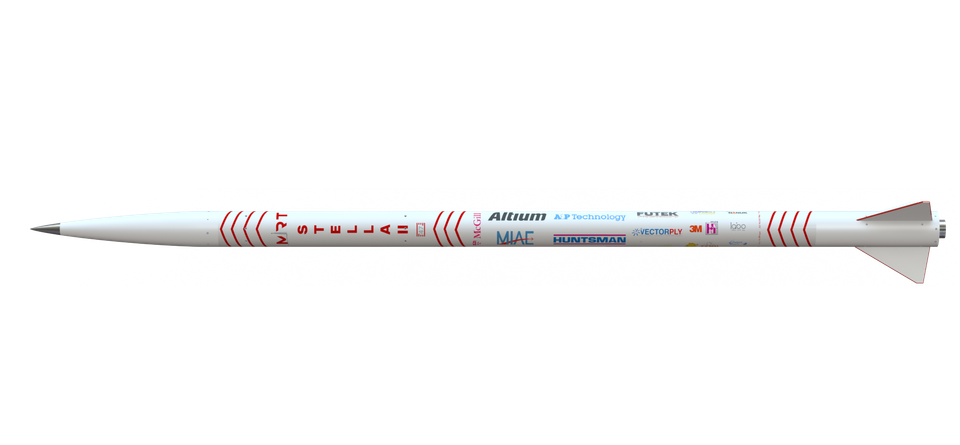
The aero-structure subsystem features a composite airframe manufactured in-houseusing a refined resin infusion process. This method was perfected over the course of the year and allows for high quality, tight dimensional tolerance composite structures as well as reduced lead times.
The avionics are centralized in a radio-transparent fiberglass airframe section, featuring triple-redundant ejection and telemetric systems. The centralized avionic section allows for rapid, convenient assembly, and easy access to theejection charges located in the forward parachute chamber.
A single separation point is located at the nose cone, which houses a payload intended to measure the pressure distribution on the cranial cavity resulting from high accelerations.
578.49 m/s
Results:
Spaceport America Cup 2018:
- 30K COTS Category: 7th/15
- Overall: 22 of 99